Leveraging data to drive cost savings in manufacturing
Tue, March 18, 2025- by Nigel Hamblin
- 6.5 minute read
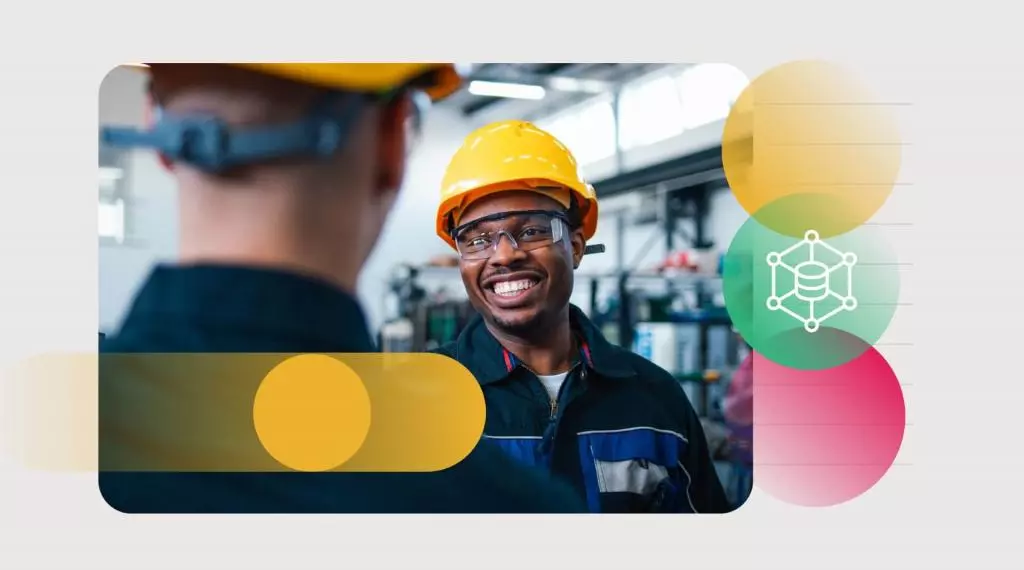
Concepts like JIT and Kaizen have transformed modern lean manufacturing with a clear, structured way to drive operational efficiency and cost savings. So why are so many manufacturers struggling to leverage data to further the continuous improvement journey?
The truth is that siloed, inaccessible, and underutilised data still hampers production efforts. With fragmented data streams across countless technologies, including machinery, ERP, SCADA, and MES, teams simply don't have the tools or time to gain a clear understanding of operational health. Decisions are reactive, and costs are often incurred by the time bottlenecks and inefficiencies are detected.
In this article, we’ll examine the problem with data in manufacturing and show how the right data approach can drive proven cost savings at every stage of production.
Manufacturing’s expensive data problem
Modern manufacturing generates massive amounts of data from sources throughout the production process. But while the potential for data-driven decision-making in manufacturing is huge, most manufacturers face challenges in accessing, integrating, and leveraging their data effectively.
The results? Suboptimal productivity, bottlenecks, unexpected downtime, and missed opportunities for savings. The issue also hampers continuous improvement, leading to a trial-and-error approach to process optimisation rather than a data-driven improvement strategy.
If one or more of the following issues sound familiar, you probably have a data problem that’s holding your factory back from achieving its full potential.
1. Data silos and a lack of system integration
At the core of the data problem in manufacturing is data fragmentation across multiple disconnected systems. Operations usually rely on a wide range of software solutions and tools, including:
- ERP (Enterprise Resource Planning) systems
- MES (Manufacturing Execution Systems)
- SCADA (Supervisory Control and Data Acquisition)
- PLM (Product Lifecycle Management) software
- IoT-enabled machinery and sensor networks
- Quality control databases
Each of these usually operates in isolation, with unique data structures and reporting mechanisms due to different base architectures and use cases. With all of this siloed data, it can be difficult to gain a unified view of operations without extensive manual cross-referencing and reconciliation.
This leads to inefficiencies such as delayed decision-making, as managers lack real-time visibility into wider production performance beyond a few key performance indicators (KPIs).
It hampers proactive problem-solving and also makes cross-functional collaboration difficult. Engineers, operators, supply chain managers, and project managers all use their own data sources, often with partial or outdated information.
This misalignment is also visible in reporting, with disparate data sources and manual collection leading to slow reports with conflicting insights and poor strategic alignment.
2. Poor data quality and inaccuracy
Data quality remains a major issue when manufacturers have access to vast sources. Inconsistencies, inaccuracies, and missing values all lead to limited analytical value and hampered decision-making. Common data quality issues include:
- Duplicate records caused by manual data entry errors or mismatched identifiers across systems.
- Incomplete datasets missing critical machine performance metrics or production tracking logs.
- Outdated information caused by a lack of real-time updates leads to production and inventory planning errors.
The consequences of poor data quality can be severe. For example, resources can be allocated inefficiently due to production schedules being based on incorrect demand forecasters. This can lead to costly issues, material shortages and overstocking, hampering your Just-In-Time (JIT) manufacturing efforts.
Meanwhile, predictive maintenance is also made more difficult due to poor sensor data. Compliance is also an issue, with reporting (i.e. carbon footprint) relying on accurate and accessible data from across the full production process.
3. Lack of real-time data accessibility
Timely data access is critical for optimising manufacturing processes and avoiding costly disruptions. However, many manufacturers still rely on batch processing and manual reporting, leading to only making data reviews at the end of shifts or production cycles.
This leads to unplanned downtime from bottlenecks, equipment failures being detected too late, and production defects only being identified after significant materials usage.
Without the holistic view of production that real-time data unlocks, quality issues quickly lead to increased waste, delayed corrective action, and higher operating costs due to energy overconsumption and labour misallocations.
4. Limited predictive capabilities
This siloed, low-quality, outdated nature of manufacturing data leads to a reactive approach to manufacturing. Historical data analysis can only tell part of the story, providing some useful insights into past performance without shining enough light on future risks and opportunities.
With the right data strategy, modern predictive analytics can be leveraged to overcome these issues, allowing manufacturers to anticipate problems and optimise processes before issues have already incurred costs.
However, implementing this level of analytics proves to be a significant challenge for many companies. Data needs to be consolidated into a unified platform, but this also means legacy data from systems which weren't designed to work with modern data lakes.
Analytics are significantly less valuable without large data sets combining historical and real-time data, yet many internal IT teams lack the resources and skills to effectively combine the two.
This leaves many manufacturers without predictive analytics that work from the full spectrum of information sources, causing high downtime rates, inefficient production scheduling, and poor supply chain forecasting.
5. Security and compliance risks
With increasingly connected infrastructures, cybersecurity and compliance have become about more than firewalls and basic reporting. Industrial control systems (ICS) are prime targets for cyberattacks, ransomware, and data breaches, which can lead to costly compliance penalties.
Without strong data security measures and automated compliance tracking, manufacturers can also fail to meet industry standards (e.g., ISO 9001, FDA regulations, or environmental compliance) due to poor governance.
Why a unified data platform is the answer
Tackling these data challenges will require a shift away from fragmented systems and manual processes towards automation and real-time processing. This necessitates using a unified platform that can clean and consolidate data from tools across the whole spectrum of manufacturing.
The platform needs to provide:
- A unified data lakehouse to provide a single source of truth across functions.
- Automated data validation tools to improve accuracy and consistency.
- Real-time analytics dashboards to support proactive decision-making.
- Predictive analytics capabilities to prevent downtime and optimise processes.
- Robust cybersecurity measures to protect industrial data assets.
- Legacy data integration to provide more insightful analytics from past trends.
With a system like this in place, all data, both real-time and historical, is connected. Data from ERP platforms, IoT-connected machinery, store sensors, and everything in between work together to deliver a 360-degree view of production health.
Performance tracking, inventory, and resource allocation can all be viewed and managed through advanced dashboards and visualisation tools, allowing leaders to detect failures before they incur unnecessary costs, reduce downtime, and automate reporting.
This level of real-time analytics also frees up valuable time for operations teams, allowing them to work proactively instead of scrambling to reactively solve issues. The result? Tangible cost savings, reduced waste, and significantly improved efficiency.
How the 5Y platform delivers cost savings
5Y is a unified data platform built on Microsoft Azure architecture that connects every tool and data stream across the manufacturing process. It automatically collects, cleans, and stores this information in a data lake for unrivalled operational health and efficiency visibility.
With everything unified into one place, you can shift from reactive to proactive data-driven decision-making. The real-time analytics and out-of-the-box dashboard and reporting capabilities of 5Y allow manufacturers to:
- Identify bottlenecks before defects occur
- Reduce waste with real-time process control
- Match demand with production capacity using AI-driven forecasting
This allows for savings at all production levels, with standard and customisable reports to analyse equipment performance, optimise costs, and more effectively plan resources.
5Y also connects with all the tools you already use or plan to use. For example, leading global chemical manufacturer AGC was struggling to extract and analyse critical equipment data from Microsoft Dynamics 365.
By implementing 5Y, they generated real-time insights into asset performance, reduced maintenance-related downtime and optimised operational efficiency.
Meanwhile, FTSE 250-listed manufacturer Rotork faced challenges consolidating production and financial data across multiple ERP systems. By adopting 5Y, they eliminated manual reporting bottlenecks while gaining real-time gross margin and order cost analysis to drive material efficiency improvements.
Since 5Y is designed to ingest real-time data from sources across all business functions, it also works with finance, supply chain, and logistics data.
This allows businesses like UK EPS manufacturer Bewi to save costs by dynamically responding to fluctuations to improve procurement planning and inventory accuracy.
Accelerate your time to value
Such a radical shift in data management probably sounds expensive and long to implement. However, you can generate insights in as little as 60 days, thanks to pre-built integrations and reports that deliver 80% of your reporting requirements.
As a prebuilt solution, there’s also no stress on internal IT teams, no lengthy development cycles, and minimal implementation costs. Meanwhile, the simple subscription model means you get exactly what you pay for from day one.
Book a demo today to learn how you can leverage 5Y to improve production quality and reduce costs.