Manufacturing KPIs: 9 Metrics You Need to Track and How to Track Them
Tue, July 23, 2024- by Paul Saxton
- 6 minute read
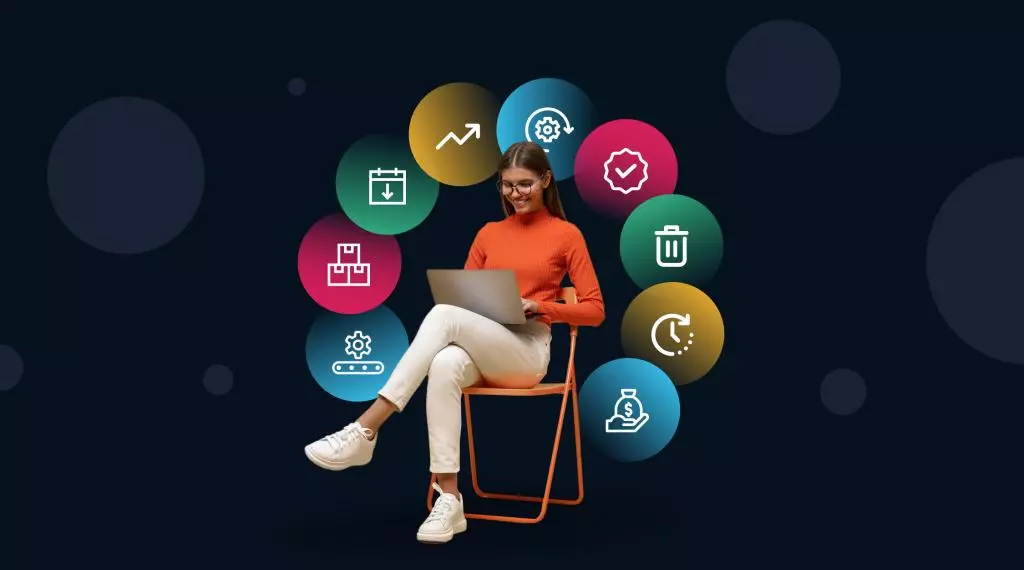
Want to quickly see what’s wrong with your manufacturing processes, what’s right and how you can improve them? Then, you need to be tracking manufacturing KPIs.
Manufacturing KPIs benchmark your business’s performance so you can track your improvements, pinpoint issues as soon as they occur and understand your financial resilience.
In this article, we’ll cover the top manufacturing KPIs you should be monitoring, how to calculate them and how to track them using industry-leading manufacturing analytics software.
What is a manufacturing KPI?
A manufacturing KPI is any well-defined metric a manufacturing business can use to gauge its performance. A KPI can measure almost anything from the volume of goods you produce and their quality to your business’s revenue and costs.
There are hundreds of KPIs you could measure. But just because you can measure something doesn’t mean you should. Rather than trying to keep track of dozens of different metrics, we recommend focusing on a select few with the following characteristics.
Your manufacturing KPIs should:
- Align with your business goals
- Be specific and measurable
- Be actionable
If KPIs aren’t relevant to what you want to achieve, there's no point in tracking them. You’re just wasting time. Similarly, you need to be able to take action after reviewing them. That can only happen if you have very specific KPIs that measure key parts of your process and flag issues that need investigating.
Top manufacturing KPIs to measure
What counts as a relevant KPI will be different for every business. But there are a few manufacturing KPIs we think everyone should be tracking.
1. Throughput
Throughput is a measure of a machine, line or plant’s production capabilities. It’s how much you can produce over a period of time and is calculated using the following formula:
Throughput = Number of Units Produced / Time
You’ll want to measure throughput in real-time wherever possible since it’s a leading indicator of equipment performance. Any issues that cause throughput to fall must be addressed immediately to prevent a knock-on effect on other KPIs like scrap rate and lead time.
2. Production volume
Production volume is the number of units you produce in a given time frame. It’s a fundamental benchmark that you can use to gauge your factory’s productivity.
Here’s how you calculate it:
Production Volume = Total No. of Products Manufactured During a Specified Timeframe
Tracking your production volume over time can help highlight progress you’ve made improving your processes. It can also highlight issues with equipment or staff that are reducing production volume.
3. Downtime
Downtime (also known as idle time or offline time) is any period of time when your machines or manufacturing processes are on hold and no products are being produced. This includes both planned and unplanned downtime.
You can calculate it by adding up all downtime over a given period:
Downtime = Sum of All Downtime During a Specified Period
You can also calculate it as a ratio of downtime to operating time:
Downtime Ratio = Downtime / Operating Time
This KPI won’t tell you what’s causing the downtime — whether that’s broken equipment, an issue caused by an inexperienced operator or pre-planned maintenance— but it’s an excellent leading indicator of productivity issues.
4. Overall Equipment Effectiveness
Overall Equipment Effectiveness is one of the best measures of manufacturing productivity.
It’s the percentage of time your plant is producing high-quality goods and is calculated by multiplying your plant’s Availability (the percentage of time you operate as scheduled) by Performance (the percentage of time your plant is working at full capacity) and Quality (the percentage of quality units you produce).
OEE = Availability x Performance x Quality
The higher your OEE, the more effective your equipment is. You’ll probably never score 100%, as it would mean manufacturing all the time at full capacity and with no defects. But there’s no harm in aiming for it.
Bear in mind, though, that like other KPIs in this list, Overall Equipment Effectiveness doesn't show the whole picture as it doesn’t take into account downtime or maintenance.
5. Work in Process
Work in Process (WIP) measures the value of goods in production that have yet to be completed. It includes the cost of raw materials, labour and overheads.
You calculate WIP using the following formula:
WIP = (Beginning WIP + Manufacturing Costs) – Cost of Goods Manufactured
WIP is a great KPI for understanding how much of your capital is tied up in the manufacturing process and whether there are any supply chain issues.
6. First-Pass Yield
First-Pass Yield (FPY), also known as first-time yield (FTY) and first-time through (FTT), is a KPI that measures your production quality and efficiency.
It is the number of units you produce without defects and no need for additional improvement compared to the total number of units produced. The formula is as follows:
FPY = Quality Items / Total Items Produced
FPY is an indicator of manufacturing issues. If it starts dropping, it could mean a problem with a machine, raw material or process. Obviously, you want to keep FPY as high as possible, as this shows that your production processes are reliable and effective.
7. Scrap rate
Scrap Rate is the opposite of First-Pass Yield. It’s a measure of the number of goods deemed defective beyond repair and is calculated using the following formula:
Scrap Rate = No. of Scrap Units / Total no. of Units
Monitoring Scrap Rate helps you understand the effectiveness of your production process and can highlight serious issues and inefficient processes. It also helps you reduce costs if you can take steps to lower your scrap rate.
8. Lead time
Lead time is the total amount of time it takes for a customer to receive their goods. You calculate total lead time by adding up the time it takes to process, make and deliver the order:
Lead Time = Order Process Time + Production Lead Time + Delivery Lead Time
There are plenty of ways to improve your lead time, such as introducing automation into your processes, eliminating unnecessary steps in your manufacturing process and reducing unplanned downtime.
9. Revenue per Employee
Revenue per employee is a profitability metric that tracks the total amount of revenue each employee generates. Here’s how you calculate it:
Revenue Per Employee = Total Revenue in a Given Period / No. of Full-Time Employees in the Same Period
It’s a great way to measure the efficiency of your manufacturing process. The higher your revenue per employee, the more efficient you become since you’re doing more with the same or fewer resources.
The easy way to track KPI data
There are several ways you can keep track of manufacturing KPIs. Using an Excel spreadsheet is common, but several issues mean this method should be consigned to history:
- Updating spreadsheets requires a lot of manual effort. That’s time your team could be spending on revenue-generating activities.
- Human error and duplicate data issues are bound to occur when inputting data into spreadsheets.
- Even when they are stored in the cloud, spreadsheets are hardly the most accessible tracking method.
Instead, we recommend manufacturers use an automated and centralised solution that solves all of these issues while also making it easier to turn insights from your KPIs into action.
Enter manufacturing analytics.
A manufacturing analytics solution like 5Y centralises and transforms data from dozens of disparate sources — whether that’s an IoT sensor or Finance & Supply Chain software — so you can track KPIs automatically. Better still, it can consolidate your most critical metrics into a single dashboard, allowing anyone on your team to track them in real time.
There’s no easier way to consolidate, track and manage all of your core manufacturing data than 5Y’s Manufacturing Analytics solution. Our Microsoft-aligned platform provides the vast majority of your reporting requirements out of the box, meaning you can be up and running in less than a month.
You aren’t left to customise the solution yourselves, either. Our data experts are on hand to build new data integrations or create custom reports as and when required. We guarantee the ongoing operability of your analytics solution for as long as you work with us.
Book a demo today to see how you can track manufacturing KPIs and transform your process using 5Y’s Manufacturing Analytics solution, or speak to a member of our team for more information.