Improving operational efficiency: A data-driven guide for production managers
Tue, March 18, 2025- by Nigel Hamblin
- 4.5 minute read
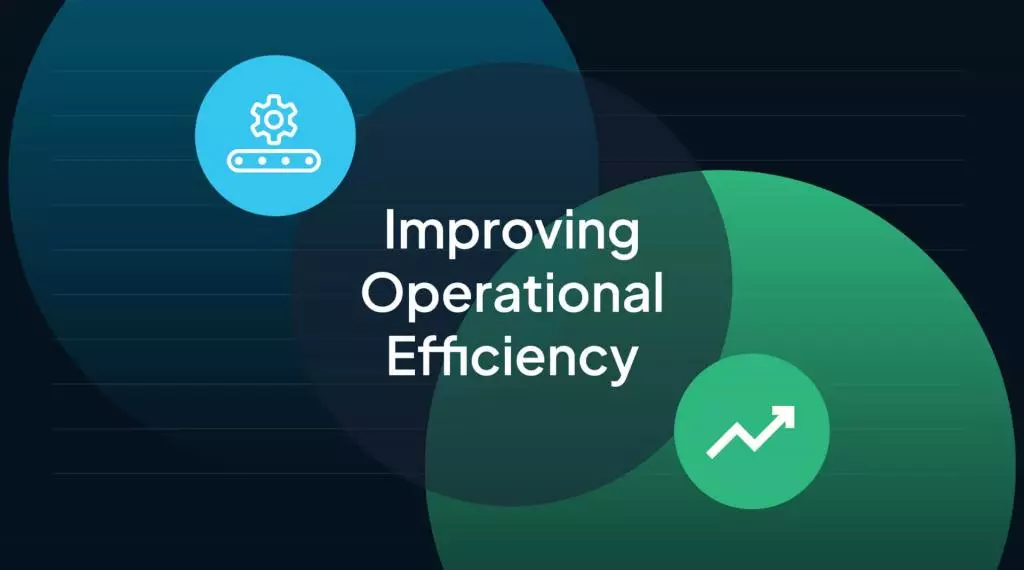
There’s one truth production managers can’t avoid: most still don’t have the data visibility they need to drive continuous improvement.
Endless spreadsheets, standalone software, and disconnected tools hamper decision-making, forcing teams to manually reconcile and cross-reference information to gain a clear picture of processes.
In this article, we’ll explore how siloed data, outdated reporting methods, and an inability to react in real time hinder operational efficiency. We’ll also examine how a centralised data platform can drive improvements across every manufacturing function.
The challenges of poor operational efficiency
Continuous improvement is at the core of modern manufacturing. However, many production leaders don’t realise that data management is holding them back from driving operational efficiency.
You’re probably familiar with the following fragmented data problems. Here’s how a unified data platform solves them:
1. Unplanned downtime due to equipment failures
Unplanned downtime is one of the most significant barriers to operational efficiency. However, many manufacturers still rely on reactive maintenance, addressing equipment issues only after a failure occurs.
While most machinery has inbuilt IoT sensors, these often feed into siloed systems that make the data visible only to front-line production teams. These systems might flag early warning signs of faults, but they’re not built to spot trends and support preventative maintenance processes.
A unified data platform like 5Y consolidates real-time machinery performance data in one place, giving everyone visibility over potential issues. Meanwhile, AI-powered analytics analyse real-time and historical data to spot wear-and-tear trends to help you create an optimised maintenance schedule.
2. Inefficient production scheduling and resource allocation
Traditional scheduling relies on static models that don’t adapt to changes like logistics issues, demand fluctuations, and machinery issues. Meanwhile, production managers often struggle to align staffing levels with demand, leading to overstaffing during slow periods and understaffing during peak production.
With AI-powered production planning, however, manufacturers can create dynamic schedules that adjust to real-time data, avoiding bottlenecks, overproduction or excessive downtime.
A unified data platform like 5Y brings production data, supply chain updates, and labour availability insights into a single platform. It allows managers to make informed decisions about resource allocation and task management, and shift scheduling based on live operational conditions rather than outdated reports.
3. Lack of cross-functional visibility
While modern systems like Enterprise Resource Planning, Manufacturing Execution Systems and IOT-connected machinery increase visibility into individual processes, these systems still silo data because they don’t connect with other tools. This leads to time-consuming manual data collection, planning difficulties, and disjointed decision-making.
Implementing a centralised data platform brings together all relevant production, financial, and operational data into a single source of truth. For example, 5Y’s unified data platform integrates ERP, MES, and supply chain management systems, giving production managers real-time access to inventory levels, order statuses, and equipment performance metrics.
4. Quality control issues
When quality issues are only detected in post-production inspections, you face higher scrap rates, rework costs, and delivery delays. But without the right insights in the right format, it can be difficult to flag defects in a proactive way.
Thanks to a modern real-time dashboard, 5Y centralises data from every factory machine and combines it with quality management systems (QMS) information and inputs from production line workers.
This gives you an unrivalled top-down view of quality across the manufacturing process, allowing you to make decisions and improvements more easily.
You can view different types of machines together, spot patterns, and cut down on manual intervention. AI insights allow you to supercharge this work by spotting patterns and recommending corrective action.
5. Poor inventory and supply chain management
Just-in-time manufacturing relies on precise inventory and supply chain management. However, getting this right can be challenging when you’re running manual checks, stock reports and cross-referencing information from multiple systems and business functions.
By centralising procurement, logistics and production data in a platform like 5Y, production managers can optimise material flow by:
- Automating reorder points based on actual usage trends.
- Tracking supplier performance to anticipate delays.
- Synchronising production schedules with incoming inventory shipments.
6. Compliance and regulatory challenges
Regulatory compliance in manufacturing is complex and time-sensitive, but manual tracking is inefficient and prone to human error. This often leads to missing records and inconsistencies.
With a solution like 5Y that automatically brings key data into one place and flags potential compliance issues, you can ensure adherence to industry regulations without disrupting operations.
The platform also has industry-leading reports ready out of the box, so in addition to a dedicated compliance dashboard, you can simply pull compliance reports rather than manually collating them.
Unlocking operational efficiency with 5Y
Many manufacturers rely on ERP (Enterprise Resource Planning) and MES (Manufacturing Execution Systems) to house data together. However, while these solutions have their place, insights from different departments are still held in siloes, and production leaders don't have a holistic view of operational efficiency with the context of both real-time and historical data.
As we’ve explored, a unified data platform like 5Y mitigates this by housing data from every source across the entire range of operations. ERP and MES data combine with information from production monitoring systems, IoT sensors, supply chain platforms, and more to create a single source of truth for unrivalled visibility.
This is stored alongside historical data from legacy systems using a data vault method to ensure preservation. This also allows modern analytics to use information from older systems in addition to real-time data from your newer tools. Since 5Y is built on Microsoft Azure architecture, it works with any new tools you might introduce down the line, giving you the flexibility to experiment.
Meanwhile, 80% of industry-leading reports and analytics are ready out of the box, decreasing time-to-value and allowing you to start generating actionable insights into operational efficiency in as little as 60 days.*
Its capabilities include:
- Production order reports. Analyse your production efficiency, spot potential issues and optimise your processes.
- Production planning insights. Build realistic schedules, improve your production processes and forecast future needs.
- Inventory transactions reports. Understand how transactions impact industry levels and accurately forecast future demand.
- Route operation analytics. Improve transport-related processes by collecting, visualising and analysing route data.
- Resource analysis and planning. Evaluate all of the current resources at your organisation’s disposal and optimise future deployment.
- Production costs analysis. Access insights into production costs and understand ways to minimise spend and budget accurately.