Eliminating the scourge of manual data collection in manufacturing
Tue, March 18, 2025- by Nigel Hamblin
- 6.5 minute read
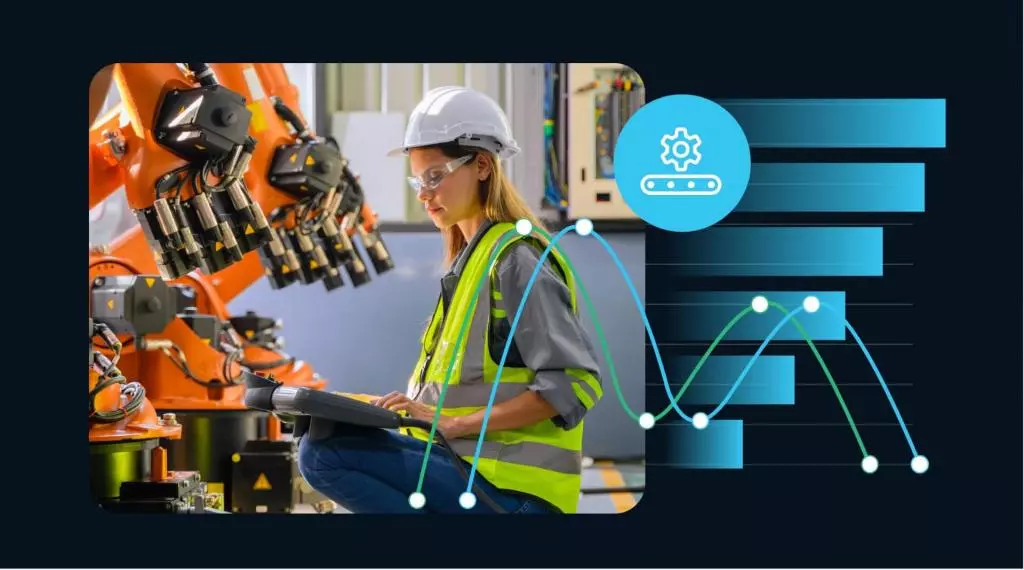
Manufacturers generate vast quantities of data they could use to drive operational efficiency and slash costs. But while the potential for data-driven manufacturing decision-making is enormous, many factories are struggling to implement it.
Manual data collection is a major hurdle.
Despite the rise of Industry 4.0 and digital transformation, many production lines still record critical data using pen-and-paper logs, spreadsheets, and disconnected legacy systems.
In this article, we’ll examine why traditional data solutions result in higher production costs, inefficiencies, and missed optimisation opportunities. We’ll also explore how modern data lakes can overcome these challenges, driving efficiency, process optimisation, and cost savings.
The problem with manual data collection
Factories all across the UK still rely on workers manually logging operational data through paper records, spreadsheets, or disconnected legacy systems.
Meanwhile, production lines generate massive amounts of data from sensors, machinery, quality control systems and more.
While this data is often digital, collating it in a cohesive format to leverage real-time insights, predictive analytics, and operational optimisations remains a huge challenge.
Many factories struggle with error-prone, siloed, and slow-moving data. Without a single source of truth that increases visibility, it becomes extremely difficult to drive continuous improvement and remain competitive.
This outdated approach leads to inconsistencies, delays, and inefficiencies that compromise production quality, increase costs, and hold back decision-making.
Human error and data inaccuracy
Poka-yoke, forcing function, behaviour-shaping constraint, whatever you want to call it — mistake-proofing is a core tenet of modern manufacturing.
So why is manual data collection still prevalent despite being inherently prone to misrecorded entries, inconsistencies, and delays?
Employees recording data manually often experience fatigue, distraction, or unclear formatting standards. This can lead to unreliable figures that can cause issues in decision-making when trying to cross-reference and analyse data.
Different teams across the business might also use different recording methods and formats. This can be down to both working practices or the unique nature of their specific machinery and tools, making it time-consuming to reconcile data and extrapolate insights.
This inefficient lack of automation leaves manufacturers with inconsistent data, which weakens process visibility, hampers forecasting, and makes resource allocation difficult.
Productivity drain and inefficiency
Even the smallest time inefficiencies lead to massively reduced production when multiplied across an entire staff force.
Manual collection can force employees to spend significant time logging, transcribing, and verifying data instead of focusing on core production tasks. It also slows reporting cycles and delays corrective actions, leading to increased operational risk and cost.
Manual cleaning and structuring are also necessary before factories can use data for analysis. This, again, wastes valuable time that could be used on value-adding activities such as process optimisation.
The issue doesn’t stop with collection, though. The lack of transparency into key data stops manufacturers from gaining accurate real-time insights into production processes. Over time, this contributes to higher operational costs and material waste. For example, poor inventory tracking leads to excessive raw material consumption, while higher defect rates become costly due to production errors going unnoticed.
It’s also easy to misallocate labour due to scheduling operating in a vacuum and not taking into account real-time variables across the full production line.
Meanwhile, inaccessible or out-of-datea performance data from machines means proactive maintenance is difficult, resulting in increased failures and delays.
Finally, since operations can’t tap into third-party data or wider business systems such as logistics information, supply chain disruptions can develop due to inaccurate demand tracking and late identification of bottlenecks.
All of this leaves manufacturers reacting to problems after they’ve already impacted production rather than proactively preventing them.
Compliance risks and audit challenges
Increasingly tight regulations such as the EU’s new Corporate Sustainability Reporting Directive (CSRD), as well as existing standards like ISO 9001, demand accurate and detailed record keeping.
However, manual data collection makes compliance management and audits incredibly time-consuming and error-prone. Reports can take weeks to compile, eating away at valuable time. Those relying on paper logs or basic spreadsheets risk:
- Incomplete records leading to regulatory gaps.
- No historical data due to lost or damaged paper logs.
- Time-consuming audits requiring manual verification of thousands of entries.
- Inconsistent reporting standards making compliant reports difficult.
Compliance failures can result in fines running into the hundreds of thousands, especially for manufacturers in highly regulated sectors such as automotive, pharmaceutical, and aerospace. This is before even considering the expensive risk of huge reputational damage.
Why traditional solutions fail
Many manufacturers try to digitise their manual collection processes by implementing basic spreadsheet tracking, standalone software, or partial automation through finicky APIs and bandaid solutions.
While these can offer incremental improvements, they’re difficult to scale and ultimately fail to address the root problem: disparate, unstructured, and inaccessible data silos.
For example, you’ll commonly see spreadsheets used for production tracking, inventory management, and performance reporting. However, since they’re inherently static, error-prone, and lack real-time data integration, they still rely on manual data entry and updates.
The inability to link these spreadsheets directly with machinery, sensors, and ERP systems makes them a temporary fix at best and a long-term liability at worst.
Standalone software, such as quality management systems (QMS), warehouse management systems (WMS), or machine monitoring software, is a step in the right direction. However, these systems still operate independently, requiring manual reconciliation and cross-referencing to generate actionable insights.
While they help in specific areas of the production process, their proprietary nature means they aren’t designed from the ground up to communicate with each other or with broader enterprise platforms used by the rest of the business ( including finance, procurement, and project management).
ERPs: A false dawn
Modern ERP (Enterprise Resource Planning) and MES (Manufacturing Execution Systems) platforms looked to solve this at first. These were advertised as hailing in a new era of data-driven decision-making. However, while they do unify data to some degree, they still present challenges.
These systems often:
- Lack seamless connectivity with all manufacturing data sources, i.e., IoT devices, legacy production machinery, and third-party applications.
- Require significant customisation and manual intervention to extract, transform, and analyse data, leading to slow adoption and ongoing maintenance costs.
- Operate on rigid data models that struggle to adapt to evolving production processes, making it difficult to implement real-time analytics and agile decision-making.
- Have integration challenges with legacy systems and don’t present a comprehensive view of manufacturing performance or offer historical context for predictive analytics.
When we zoom out and look at the big picture, these systems have often become part of the very problem they were designed to solve.
They unify data —but into siloed clusters rather than a lake that holds the full spectrum of business information in a single source of truth.
They’re also not scalable as you evolve, experiment, or implement new software and production tools, making them a roadblock to future operational efficiency as you grow.
How to transform manufacturing efficiency with a data lakehouse solution
Implementing a centralised data lake is a proven and effective way to automate data collection and eliminate the inefficiencies of siloed systems.
Unlike traditional databases that require structured data, a unified data platform like 5Y can ingest raw, unstructured, and structured data from every tool across the full spectrum of operations.
ERP, MES, supply chain, IoT systems, and more all feed into a single platform, creating a single source of truth that’s visible to stakeholders at every level of the business.
This doesn’t stop at the production line. Tools across finance, HR, project management, and even 3rd party external logistics can all feed into 5Y, providing a comprehensive, real-time, and holistic view across all operations.
For legacy systems that weren’t built with modern data management in mind, a data vault is created to store historical data alongside real-time data from modern tools.
With everything in one place, 5Y guides manufacturers up the data maturity curve with powerful real-time dashboards and advanced predictive analytics.
80% of industry-leading reports and dashboards are also ready to go straight out of the box. This, combined with the fact that 5Y is built on the Microsoft Azure architecture, means that generating these actionable analytics is achievable in as little as 60 days, 50% faster than custom builds.*
As well as capturing and managing all data automatically, you can add and connect new tools as you see fit without additional development.
Finally, since 5Y uses a simple subscription model as opposed to expensive up-front costs, you can halve your data engineering costs* versus expensive in-house or custom platforms.
Transforming manufacturing with data-driven decision making
The reliance on manual data collection is the largest remaining bottleneck stopping fully optimised manufacturing operations.
As digital transformation and industry 4.0 continue to transform production, properly leveraging the insights available from these technologies will be key to remaining competitive, saving costs, and driving continuous improvement.
Learn more in our whitepaper.
*The “80% analytics-ready” figure applies specifically to engineering tasks such as data ingestion, integration, and preparation. The 50% faster implementation and 50% reduction in engineering costs are based on our observed averages across typical client projects. Actual results may vary depending on project scope, data quality, and unique business requirements.